What is a fibreglass truck body?
Companies use fiberglass truck bodies for refrigerated, freezer, dry, and insulated trucks. They feature XPS or PU foam cores in a sandwich structure. Additionally, popular options include PP honeycomb panels, plywood, and PET sandwich panels.
In refrigeration and insulation, XPS and PU are the best alternatives to traditional insulators.. For dry cargo, where insulation isn’t needed, we use plywood or PET sandwich panels. Fiberglass is a high-performance material for box truck construction. It has no external seams or rivets, which makes it more attractive. It is easy to finish and resistant to corrosion.
Fiberglass truck bodies are for small trailers, box trucks, and semis. You can make them in lengths from 2.5 to 12 meters. They are lighter and more durable. PU and XPS foam increase the heat insulation and reduce the gross weight. FRP has three advantages. It is low-cost, eco-friendly, and requires little maintenance. FRP foam panels can replace aluminum alloy and galvanized steel panels. They have a longer service life. We provide 100% customized body and CKD case delivery.
We offer you a full set of body or panels with complete kit options.
9 Benefits Of Using Fiberglass In Box Trucks
Fiberglass is suitable for refrigerated, freezer and dry trucks, if you are looking for high-strength material, then FRP skin must be a good choice. It is characterized by strong tensile strength, lightweight and beautiful appearance. Suitable for use in box body where the required temperature is -30℃-60℃. it is the best choice for closed box truck.
Good thermal insulation: fibreglass panels with PU and XPS foam. They make the insulation performance high.
- Waterproof: FRP panels and coatings can block water vapor and moisture.
- Low cost: FRP is stronger and cheaper than stainless steel and aluminum.
- Easy to clean: With only regular maintenance and care, the service life can be up to 10 years and 50,000 hours.
- Lightweight: Using fiberglass can reduce weight. It saves diesel fuel and boosts efficiency. So, it is now a common material in many industries.
- Impact resistance: It resists impact damage and holds its shape.
- Beautiful appearance: The FRP surface has a luster. It is beautiful and will not chip off.
- Flame retardant: It can have the effect of a flame retardant (to prevent the spread of fire).
- Corrosion resistance: It is not easy to rust or corrode in the harsh environment.
Panels For Refrigerated Truck Body

Fiberglass XPS Foam Panels
Features:
Good moisture resistance, non-absorbent, good thermal insulation, lightweight, closed cell ratio ≥99%
Width: ≤3200mm
Thickness: 10-120mm
Length: ≤12000mm
Density: 35~50KG/cubic meter
Process: CNC machining, RAL color appearance.
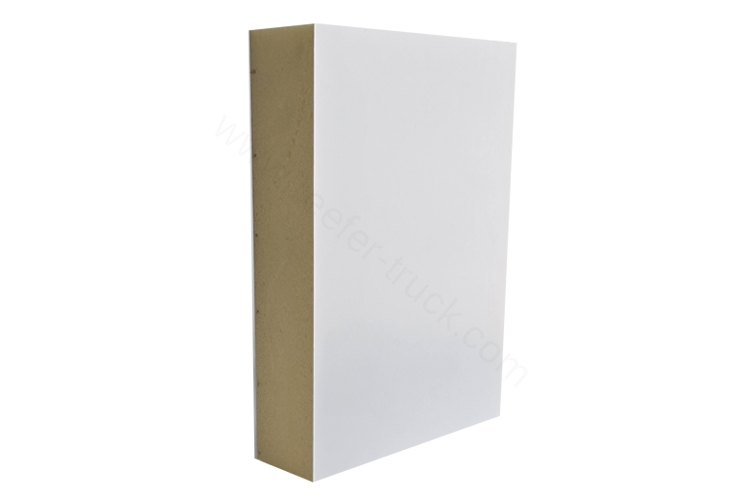
Fiberglass PU Foam Panels
Features:
Best thermal insulation, good resistance to water absorption, strong compression resistance, thermal conductivity 0.022-0.033W/(m*Κ)
Width: ≤3200mm
Thickness: 10-150mm
Length: ≤12000mm
Density: 35~45KG/cubic meter
Process: CNC machining, embedded structure
Panels For Dry Truck Body
Fiberglass PP Honeycomb Panel
Features:
high strength material, strong pressure resistance, waterproof and moisture-proof, recyclable
Width: ≤3200mm
Thickness: 10-75mm
Length: ≤12000mm
Density: 80~200KG/m3
Process: CNC machining, UV resistant coating, flame retardant coating.
Fiberglass Plywood Panels
Features:
good weather resistance, waterproof, high strength material, impact resistance
Width: ≤3200mm
Thickness: 10-150mm
Length: ≤12000mm
Density: 35~45KG/cubic meter
Process: CNC machining, embedded structure
Fiberglass PET Panel
Features: recyclable material, heat resistant, high strength material, light weight
Width: ≤3200mm
Thickness: 10-150mm
Length: ≤12000mm
Density: 50~300KG/m3
Process: CNC machining
Services we offer:
1:We provide high-quality fiberglass truck bodies. We offer high-performance FRP truck bodies, delivered in CKD cases.
2: Provide the best fiberglass composite panels. We supply FRP panels for fully enclosed vans for various uses.
3:We support over 50 brands, including Ford and Hino. For free design, please contact our Carbody expert.
Kits are optional:
Wall panels
Floors
Cargo E-track
Side door
Edge and corner laps
Door frame
Lock and hinge
Multi-temperature zone
Subframe
Refrigeration unit
Rear bumper
Side guardrails
Meat hanging rail system
Parameters
FRP/GRP XPS PU Composite Sandwich Panel for Reefer Body
Parameter | Specification |
Total Thickness | 50mm (Customized range: 10~120mm) |
Core Material | XPS, PU, PP Honeycomb, Plywood |
Color | Product color (Regular: Black & White, Customized available) |
Surface Treatment | Anti-UV Film |
K Value | 0.027 W/(kg·m²) |
FRP Surface Treatment | Glossy, Embossed |
Maximum Width | 3200mm |
Maximum Length | 12000mm |
External Sheet | FRP Sheet 2.00mm (Customized: 0.7~5.0mm) |
Area Weight | 8.93kg/m² |
Note:
The FRP foam panels are 50 mm thick (customizable from 10 to 120 mm). Their core materials include XPS, PU, PP honeycomb, and plywood. The standard colors are black and white, with custom colors available. An anti-UV film treats the surface, and the FRP surface can appear glossy or embossed. It has a thermal conductivity (K value) of 0.027 W/(kg·m²), a maximum width of 3200 mm, and a maximum length of 12000 mm. The external FRP sheet thickness is 2.00 mm (customizable from 0.7 to 5.0 mm), with an area weight of 8.93 kg/m².
Installation requirements:
Easy to install. You can fix it with metal profiles. We can install the CKD case delivery per the drawings. The panels have border links for convenience.
Tools: forklift, hand truck, crane, and other equipment
Assembly tools: pneumatic screwdriver, wrench.
Number of people: 1-2 people