Best Fiberglass Plywood Sandwich Panels Manufacturer
Fiberglass Plywood Sandwich Panel
Fiberglass plywood sandwich panels are a very strong material. They have many layers of thin wood and fiberglass sheets. FRP is a mix of glass fibers and resin. It is formed by laminating with an adhesive.
Fiberglass plywood sandwich panels have many advantages. We laminate both sides of the plywood with FRP. The plywood core is usually 3-11 layers of mahogany, poplar, willow, eucalyptus, and camphor. It’s 10-30 mm thick. It has high compressive and load-bearing capacity. It is resistant to deformation and rupture. It is scratch- and corrosion-resistant. It has good heat preservation performance and high sound insulation performance. Use FRP plywood in refrigerated trucks, dry trucks, RVs, houses, containers, farms, and other uses. We are the top fiberglass plywood sandwich panel supplier. We offer free design, CNC machining, and 100% customization.
Advantages:
- It’s not easy to rot.
- Good heat insulation performance.
- High-strength material
- Visual aesthetics
- High-quality production process
- Sustainable
Product Description:
Carbody’s fiberglass plywood sandwich panels are a high-performance, attractive material. They are easy to CNC and cut. The thickness of the panel can be 9-30 mm, and the plywood can be up to 3-11 layers. Outside, 2 layers of FRP sheet can protect the plywood. They are scratch-proof, waterproof, and stain-proof. It can resist UV rays and corrosion. FRP is a high-performance mixture to make the panel.
Our products allow 100% customization. You can change the fiberglass sheet’s thickness, width, color, surface, and anti-slip treatment. All of them can realize the functions and usages you want. It is ideal for special cases, including pressure-resistant, corrosive, and high-frequency areas.
In the past, pure plywood was easy to bend, corrode, and decay. It had poor waterproofing and low-pressure resistance. FRP plywood is a great replacement. It is both waterproof and corrosion-resistant. It also has better strength than pure plywood.
Comparison of FRP plywood sandwich panels and pure plywood:
Performance Index | FRP Plywood Panel | Pure Plywood |
---|---|---|
Weight | Lightweight, easy to transport and install | Heavier, increases transportation costs |
Strength | High strength | Lower strength, prone to damage |
Weather Resistance | Waterproof, moisture-proof, UV-resistant, corrosion-resistant | Prone to moisture, limited durability |
Lifespan | Long lifespan | Shorter lifespan, requires frequent maintenance |
Surface Options | Diverse: smooth, anti-slip, high-gloss, matte, etc. | Basic and limited |
Price | Cost-effective in the long term | Higher maintenance costs |
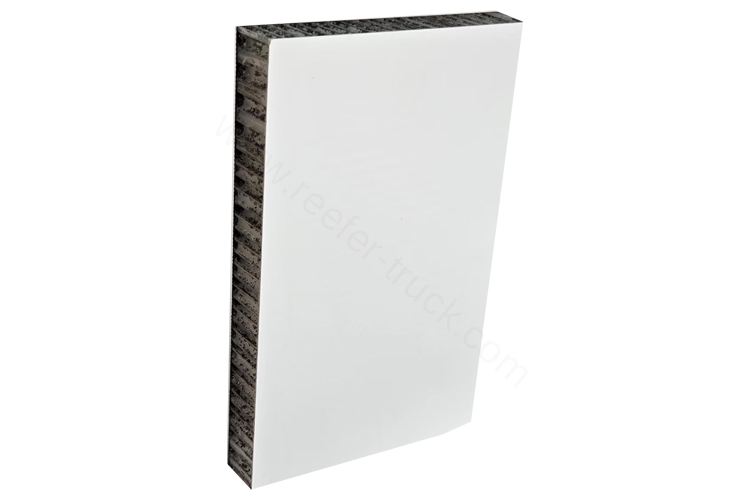
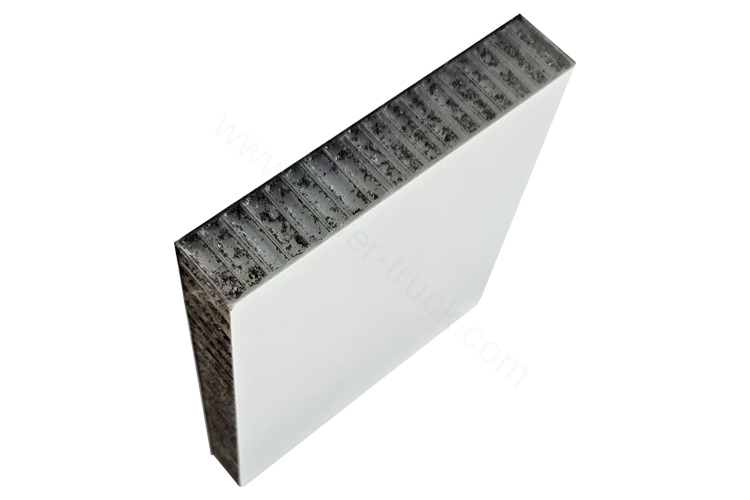
Customized Specification:
Specification | Description |
---|---|
Length | 2440mm, 3050mm, or customizable |
Width | Typically 1220mm, or customizable |
Core Material Options | Redwood, poplar, willow, eucalyptus, camphor |
Thickness | 9~30mm |
FRP Skin Thickness | 0.7mm, 1mm, 1.2mm, 1.5mm, 3mm, 5mm, or customizable |
Plywood Thickness | 5~30mm |
Plywood Layers | 3~11 layers, or customizable |
FRP Surface Options | Anti-slip finish, pebble texture, smooth surface |
Color Options | Default white, optional black, gray, red, blue, etc. |
Gel Coating | Optional gel coating or non-gel coating |
Bending Strength | 36.967 MPa (based on a sample size of 300x100x14) |
Applications:
Manufacturers use FRP plywood sandwich panels in refrigerated trucks, dry vans, RVs, and homes. It’s also used in containers, farms, furniture, campers, and door panels.
Manufacturers use it in scenes that need high strength, anti-corrosion, and waterproofing. This meets the needs of various industries.