Structural Fiberglass PP Honeycomb Panels Supplier
Fiberglass PP Honeycomb Panels
Thermoset FRP PP honeycomb panels are strong, flat, and lightweight. They are composite panels made of a thermoset FRP sheet or a thermoplastic CFRT sheet.
They have a honeycomb-shaped sandwich layer. The “honeycomb” shapes the sandwich layer. It has greater compressive strength and stability and is lighter in density.
It has many applications in cold regions. These include refrigerated and long-distance truck bodies, construction materials, and aerospace. It is also used for building modules.
Advantages:
- Low weight and density of 80 kg/m³
- PP honeycomb core is a 100% recyclable material.
- High-performance material
- Long service life
Product Description:
FRP honeycomb panel structure: It has 2 fiberglass skins, or 1 each of FRP and thermoplastic CFRT. It has a “round” PP honeycomb core in the middle. To make it more stable, you can reinforce it with other materials, like aluminum, wood, or steel. We support 100% customization.
FRP honeycomb panel is a special composite. It has a thermoset fiberglass surface. A PP core, laminated with adhesive, forms the core. You can use a non-woven fabric link to improve adhesion and stability.
FRP sheet has many advantages for honeycomb panels. It is very strong. It holds its shape under pressure and resists scratches. It also has a stable structure. It also has high chemical and UV resistance and is waterproof and heat resistant.
We use black or white as the main color of our FRP skin, and we can also use other layers. Other surface layers are available. We can customize a non-slip FRP honeycomb panel. Matte honeycomb panel, and so on.
They make the honeycomb core from round, polypropylene plastic. Manufacturers produce it using thermoplastic synthetic resins. This material is friendly to the environment and can be recycled. It is very durable and is a high-strength material. It has the advantages of corrosion resistance and high-temperature resistance.
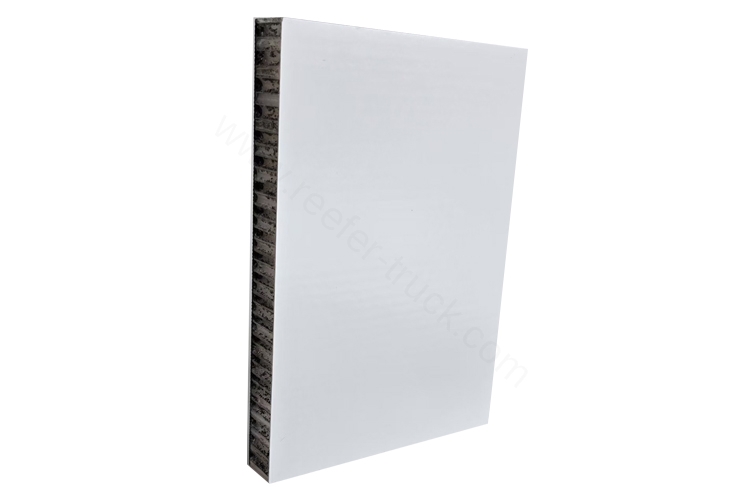
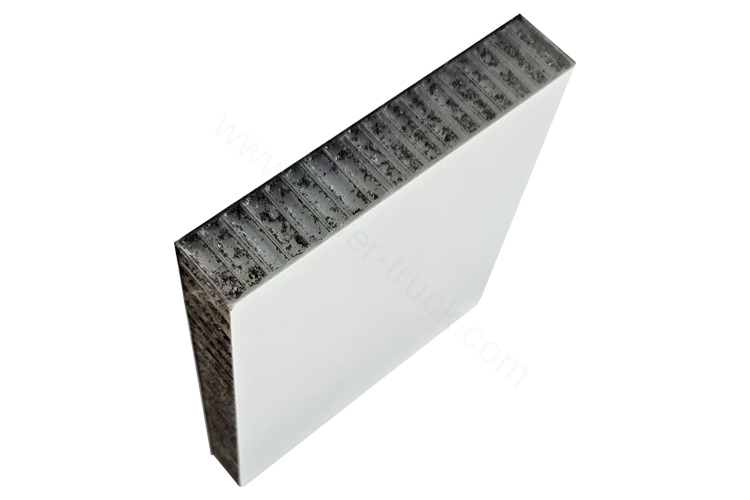
Customized
OEM/ODM Customized Processing:
Carbody offers highly customizable solutions and provides free designs.
CNC cutting and engraving of various shapes.
Internal structural enhancements
Colour options are available.
Customized surface patterns
100% customizable width, thickness, and height of the skin or core.
Support gel layer, pebble surface, smooth, non-slip, and other finishes.
Characteristics:
Carbody uses FRP PP honeycomb panels to make truck bodies. They have many advantages, despite their low density. They are stronger than traditional honeycomb panels. The lightweight materials market favours them. We have the following advantages:
- Good anti-vibration effects.
- Lightweight
- Not easy to deform.
- Waterproof and moisture-proof
- Good corrosion resistance.
- High strength
- Chemical resistant
- Easy to process
- High-pressure pressing process with a long service life.
- Pressure resistance of up to 50 MPa.
Parameters
Parameter Category | Description |
---|---|
Skin Material | FRP Sheets or CFRT Sheets |
Core Material | Polypropylene Honeycomb |
Total Thickness | 10~75mm, customizable thickness available |
Thickness Tolerance | ±0.5mm |
Panel Thickness | 0.3~5mm, customizable for higher thickness |
Core Size | 6~16mm (circular honeycomb structure) |
Standard Width | 2160mm / 2300mm / 2500mm / 2750mm (customization available) |
Length | Up to 12m, customizable length |
Density | 80~200kg/m³, adjustable based on specific requirements |
Surface Treatment | Non-slip, high gloss, matte, or other finishes with gel coat options |
Surface Color | Black, white, wood grain, stone grain, and other customizable colors |
Performance | Anti-UV coatin+A4:B13g, flame retardant coating, protective film available for added durability |
Applications:
Reefer truck body: used for cold chain transport in cold areas. It has a strong, stable body and great insulation.
Dry truck body: a strong, durable, stable structure for transport.
Building materials:can be modular building partition walls that are lightweight and possess high strength.
Lightweight aerospace materials: stable, lightweight, and used for aircraft interiors, bulkheads, and other structures.