Carbody uses advanced technology to combine FRP sheets with high-efficiency thermal insulating PU foam to produce lightweight, high-strength and excellent thermal insulating FRP skin sandwich panels, which are specially designed for vehicles with high thermal insulation requirements such as refrigerated trucks.
Panel Structure
- Ouertmost Layer: Gel coat (can be customized)
- Upper and Lower Surface Layers: Fiber Reinforced Plastic (FRP), compose of thermosetting resin and short glass fibers
- Core Layer: Polyurethane (PU) foam
- Width: 3.2m
- Length: 12m
- Thickness;10~150mm
Description
Advantages
- Heat Insulation: PU foam has the smallest thermal conductivity among all types of foams with the same density, which means it has the best thermal insulation effect.
- High Strength: The FRP skin of the panel is composed of short fibers and is isotropic, which can make the whole board bear the force evenly and enhance the overall strength of the refrigerated truck box.
- Easy to Process: FRP sheets and PU foam are both easy-to-process materials. Combined with our professional and precise five-axis CNC processing machines, we can efficiently produce integrated composite panels of the required shape for you.
- Surface Treatment: Depending on the specific application of your refrigerated truck, we can also adhere a layer of UV-resistant gel coating to the FRP skin to improve the weather resistance of the panel.
Expert in Refrigerated Truck Body Insulation Composite Panel Solutions
CarbodyGroup specializes in manufacturing high-quality box truck body composite panels, which combine strength, quality, beauty and environmental protection. We use advanced materials and technologies to improve vehicle durability, safety and transportation efficiency, and provide you with high-quality products that exceed your expectations and meet high standards.
We offer custom manufacturing services to tailor the most appropriate composite sheet solution to the customer’s specific specifications, performance requirements and application scenarios.
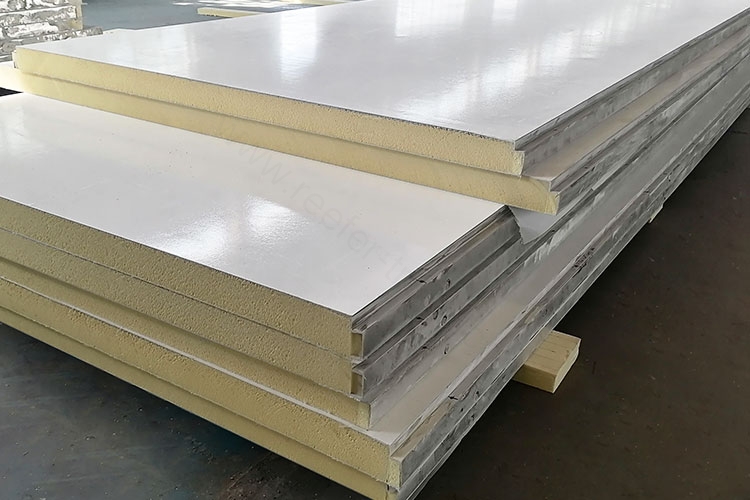
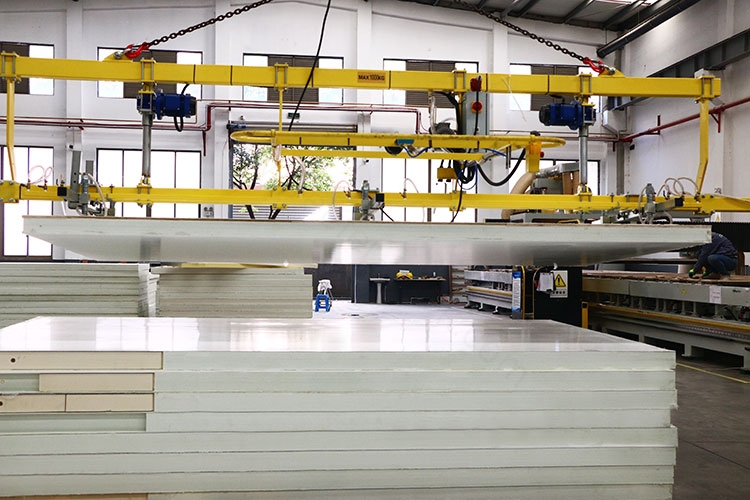
Materials and Applications
Core Materials | Skin Materials | Applications |
XPS (Extruded polystyrene) Foam | FRP(fiberglass reinforced) Sheet, CFRT(Continuous fiber reinforced thermoplastic) Sheet. | Refrigerated Trucks, Dry Freight Trucks. |
PU (Polyurethane) Foam | FRP(fiberglass reinforced) Sheet, CFRT(Continuous fiber reinforced thermoplastic) Sheet. | Refrigerated Trucks |
PVC (Polyvinyl chloride) Foam | FRP(fiberglass reinforced) Sheet ,CFRT(Continuous fiber reinforced thermoplastic) Sheet, ACP Panel(aluminum composite panel). | Refrigerated Trucks, Dry Freight Trucks. |
Composite Panel Production Lines
Our company is equipped with multiple sets of advanced integrated composite board production lines, which can efficiently complete various production process requirements such as vacuum bonding and thermoplastic lamination. The maximum length of the board can reach 12 meters and the maximum width can reach 3.2 meters.
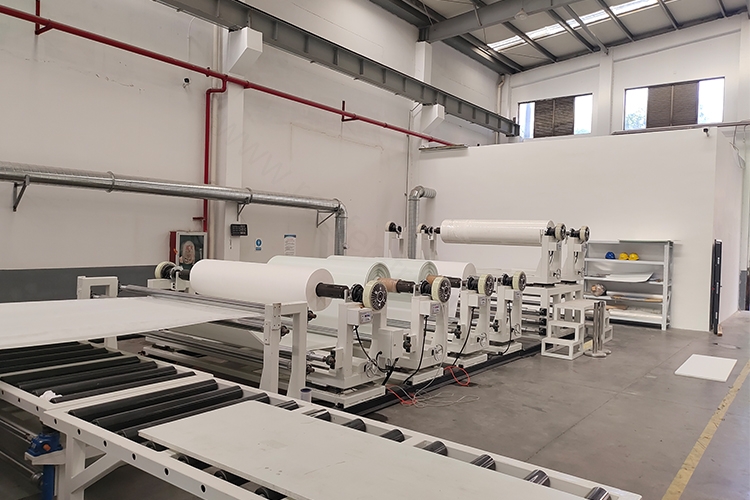
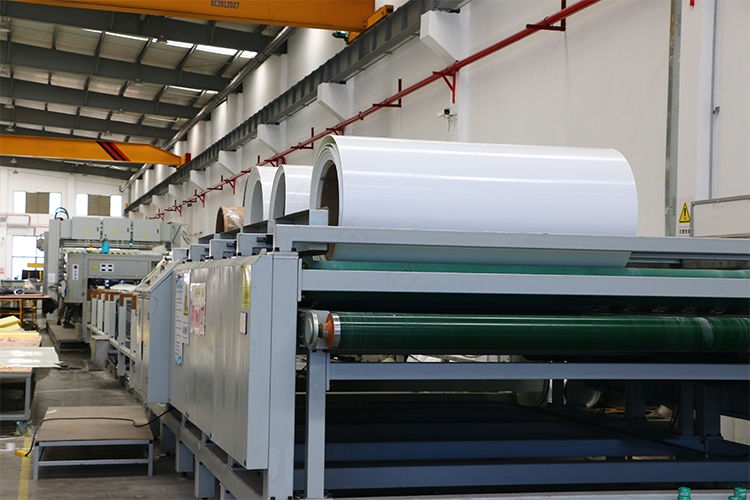
CNC Processing
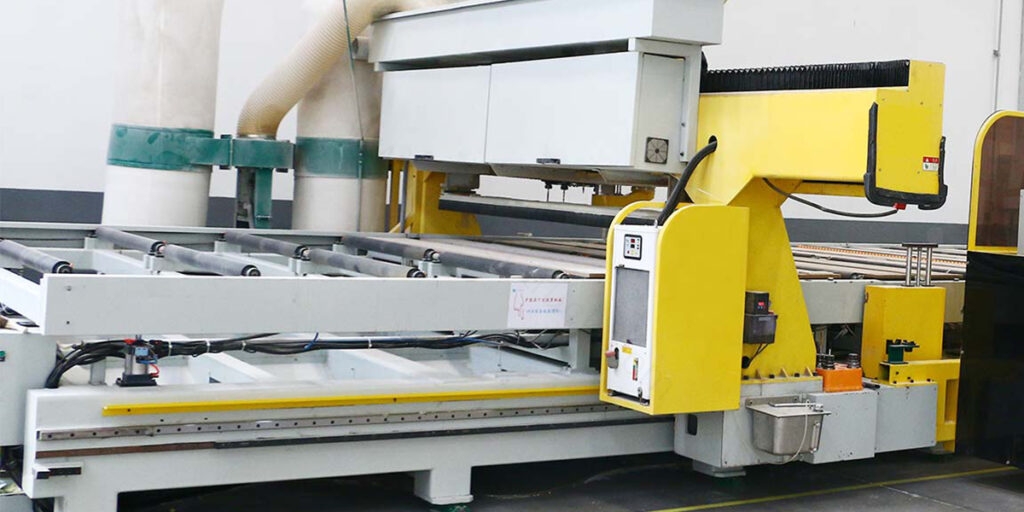
Composite panels can be customized with high speed and high precision on advanced large-scale CNC machining platforms to precisely conform to the shape required by the design. Strict control of machining parameters and efficient process management ensure that all panels produced in the same batch achieve and maintain a consistent standard of excellence and precision.
Parts Processing
We offer standard parts and non-standard parts designed to meet specific application requirements, including precision sheet metal fabrication, high-precision laser welding, custom cutting and machining of aluminum profiles, and metal casting processing.
Truck Body CKD/SKD Services
CarbodyGroup offers customized refrigerated truck bodies in both CKD (completely knocked down) and SKD (semi-knocked down) forms.
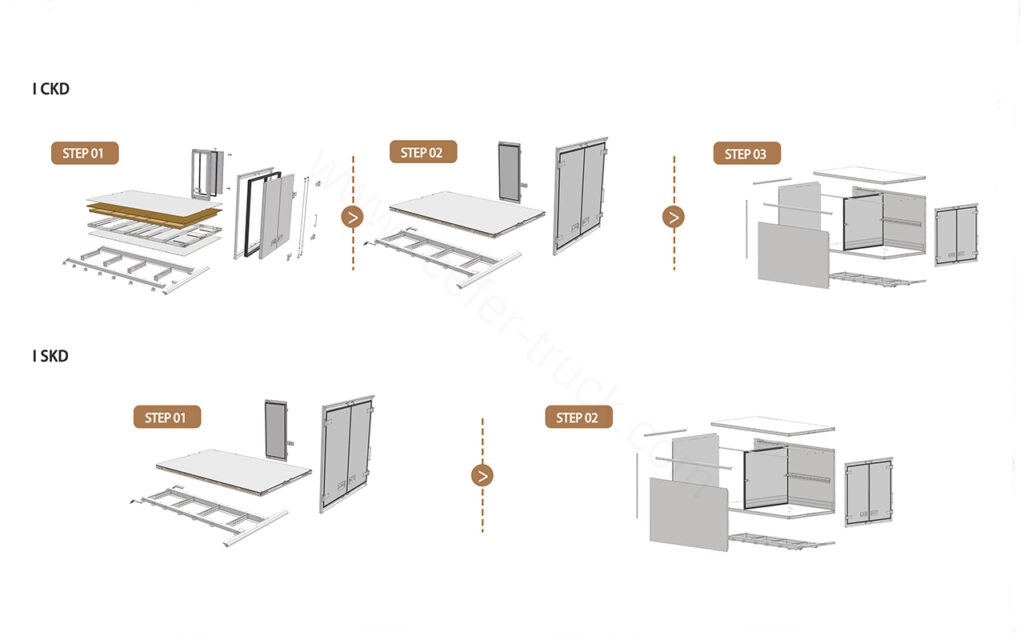
- CKD (Completely Knocked Down): For customers who want deep customization and full control over the production process, CARBODY provides a complete set of refrigerated truck body parts, including but not limited to insulation materials, frame structures, refrigeration system components, etc. Customers can assemble according to their own needs.
- SKD (Semi-knocked-down kits): The SKD solution provides some pre-assembled modules, such as integrated refrigeration units and insulation compartment main frames, which greatly reduces the complexity and time cost of field assembly. Customers only need to perform simple assembly and troubleshooting to quickly put the vehicle into service, making it an ideal choice for those seeking quick time to market and efficient logistics management.
Our professional design team provides customized design services from model planning, selection of insulation materials, optimization of cooling efficiency to compartment layout design. We use advanced CAD / CAM technology to carry out accurate modeling and simulation analysis, to ensure the rationality of the design scheme, economic and environmental protection, to help customers create efficient, energy-saving, environmentally friendly cold storage logistics solutions.