Fibreglass Reinforced Plastic (FRP) refrigerated truck bodies are excellent in cold chain logistics due to their excellent thermal insulation and light weight and durability, CarbodyGroup, as a professional CKD/SKD refrigerated truck body manufacturer, provides a series of design and manufacturing solutions to meet the application requirements of different industries.
Description
Refrigerated Truck CKD Kit Solution
The CKD (Completely Knocked Down) refrigerated truck body manufacturing process is an efficient and economical production method, which refers to the complete disassembly of the refrigerated truck body into precision parts, followed by fine packaging to ensure safety and integrity during transportation. These parts are then shipped to assembly plants around the world to be reassembled into complete refrigerated truck bodies to meet the specific needs of the local cold chain logistics market.
CarbodyGroup focuses on producing a variety of CKD refrigerated truck bodies, aiming to provide customized cold chain logistics solutions for global customers. We deeply understand each customer’s unique needs in transportation efficiency, cost control and cargo preservation. Therefore, we can not only provide standard CKD refrigerated truck body options, but also design and produce customized products based on the customer’s specific budget, operation scale and cargo characteristics.
By adopting the CKD manufacturing process, CarbodyGroup not only helps customers reduce the logistics costs of long-distance transportation, but also speeds up market response, allowing customers to adapt to market changes more quickly and seize business opportunities. At the same time, this flexible production method also promotes the effective use of resources, reduces waste and environmental impact, and conforms to the concept of sustainable development.
CarbodyGroup, with its excellent CKD refrigerated truck body manufacturing process and comprehensive cold chain logistics solutions, is committed to creating greater value for global customers and promoting the sustainable development of the cold chain logistics industry.
Structure Design
- One-piece composite panels: FRP panels usually adopt one-piece molding technology, with the middle layer of thermal insulation foam and the outer layer of weather-resistant food-grade FRP plate.
- Insulation layer design: The thickness of the thermal insulation panel is generally between 75-100 mm, which is adjusted according to the different requirements of the transported goods to ensure the best thermal insulation performance.
- Seamless connection: Seamless connection technology is used to prevent cold air leakage and improve insulation efficiency.
Truck Body Materials
- Fiberglass Polystyrene Foam Sandwich Panel.
- Fiberglass Polyurethane Foam Sandwich Panel.
Features
- Optimized design.
- Quick assembly.
- Thermal insulation.
- Durable.
- Waterproof and moisture-proof.
- Reduce manufacturing costs.
Application Scenario
- Fresh Food Transportation: including vegetables, fruits, meat and seafood, etc., to maintain freshness and taste.
- Pharmaceutical Cold Chain: ensure the safe transportation of sensitive pharmaceutical products such as vaccines and blood products in low temperature environments.
- Special Item Preservation: such as artworks, high-tech products, etc., which require strict temperature control.
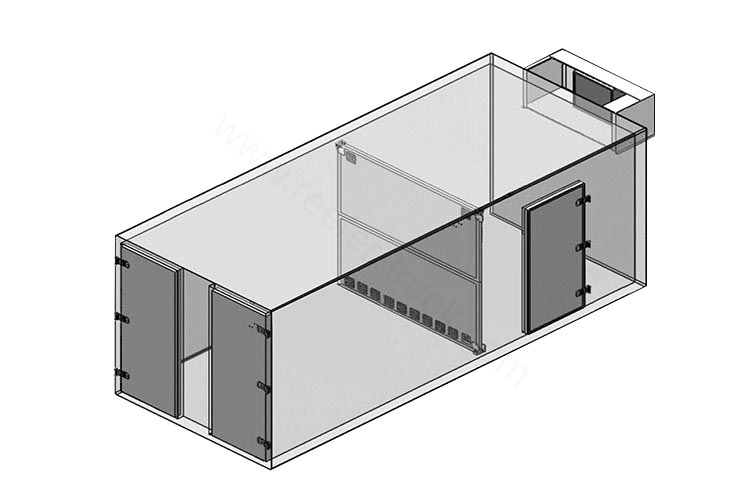
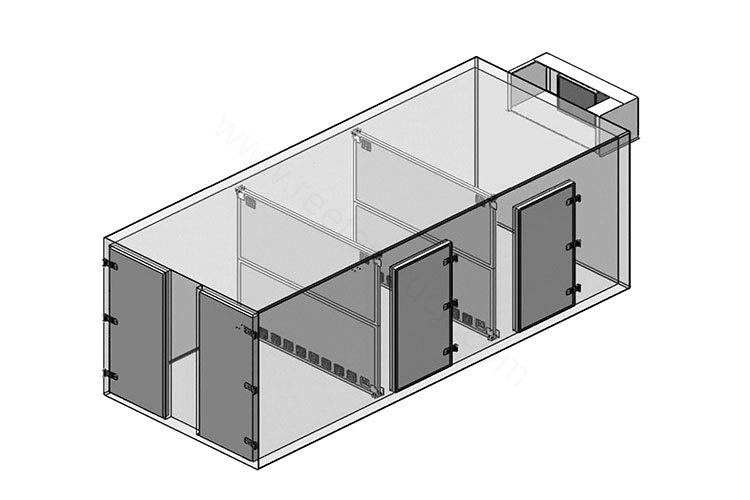
Fast Assembly, Efficient Output
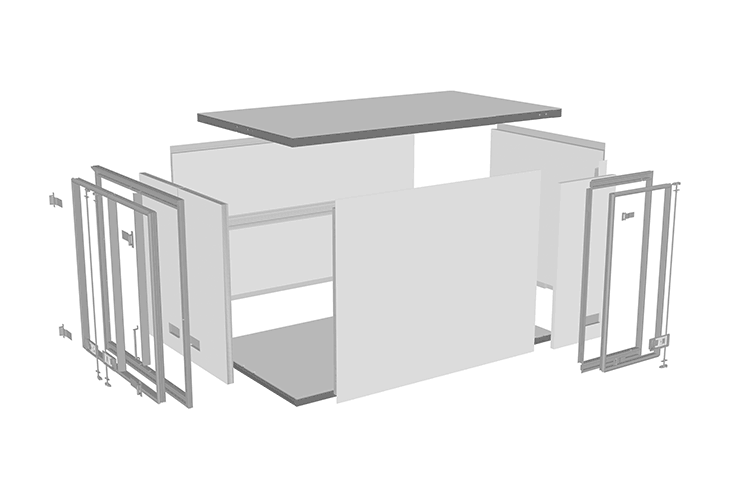
Fiberglass Sandwich Panel Of Refrigerated Truck
We offer two high-performance insulation composite panel options: XPS (extruded polystyrene) insulation board and PU (polyurethane) foam sandwich panel, designed to meet the diverse needs of different application scenarios. Buyers can flexibly choose the appropriate density, thickness and other customized specifications according to specific project requirements to ensure the best insulation effect, structural strength and cost-effectiveness.
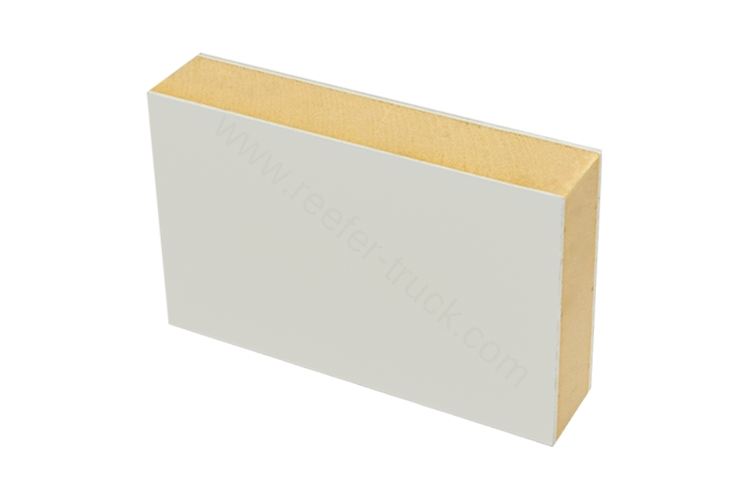
XPS Insulation Panels
- Thermal insulation.
- Not easy to deform.
- Lightweight.
- Waterproof.
- Durable.
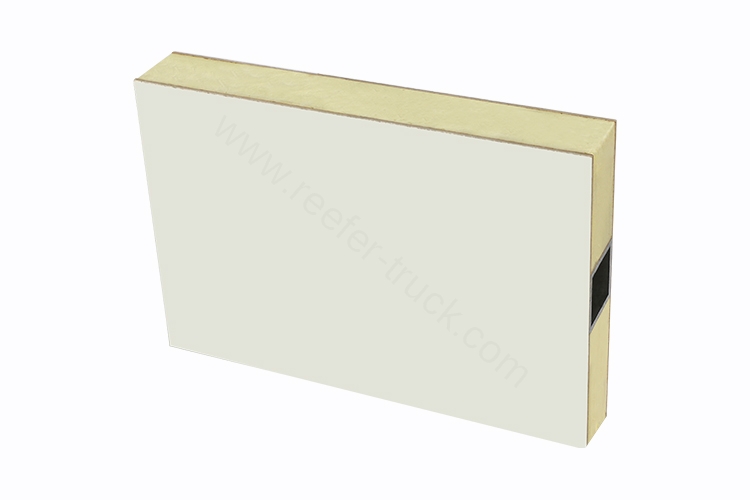
PU Insulation Panels
- Lightweight.
- Low thermal conductivity.
- Corrosion resistant.
- Waterproof.
- Compression resistant.
- Flame retardant.
High-quality Thermal Insulation Materials & Advanced Production Technology
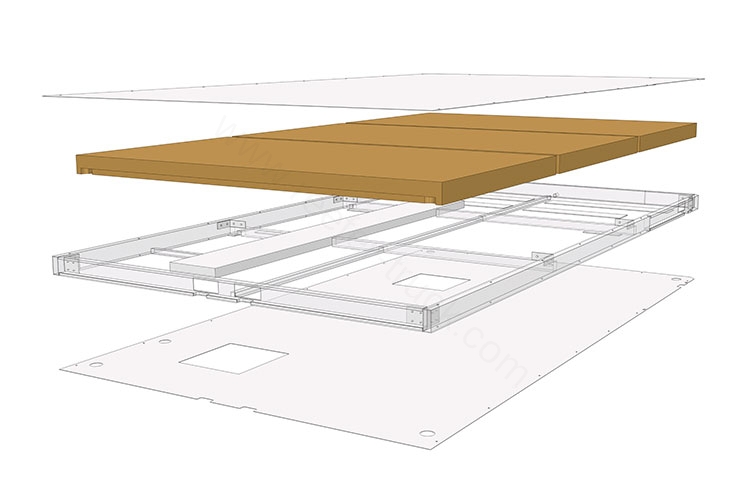
Our Refrigerated Truck CKD Kits
We focus on the unique needs of our customers and carefully design and manufacture a full range of refrigerated truck parts solutions. Here is an overview of some of the customized refrigerated truck body parts we can provide:
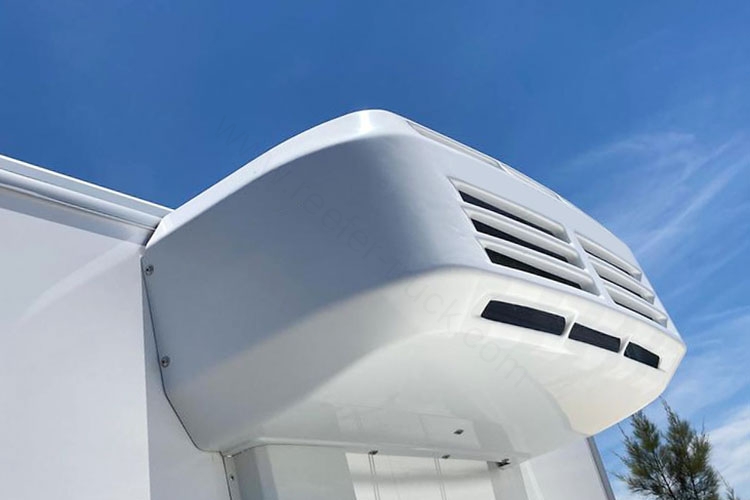
High-efficiency Refrigeration unit
Customized selection ensures that the goods maintain the optimal storage temperature during transportation.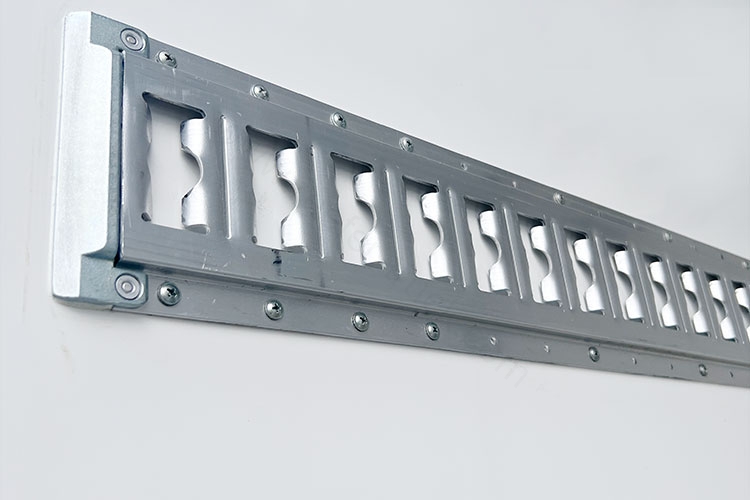
E-track Fixing System
Flexibly install various types of shelves and fixing devices to improve loading efficiency.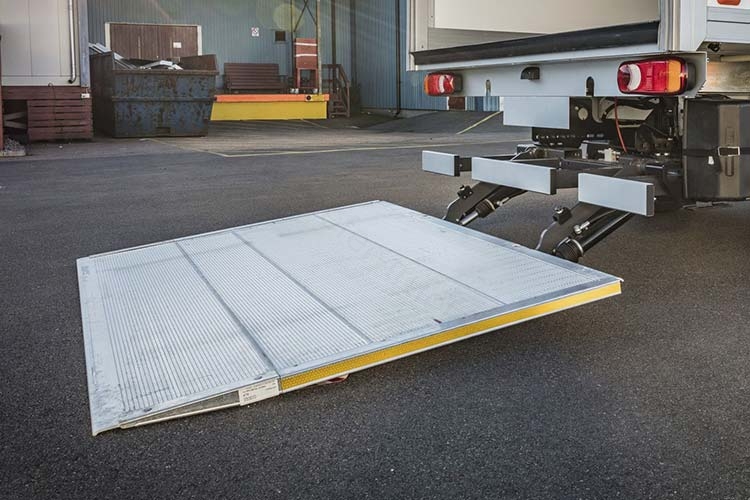
Rear Door Lifting Platform
Automated design simplifies loading and unloading process and improves work efficiency.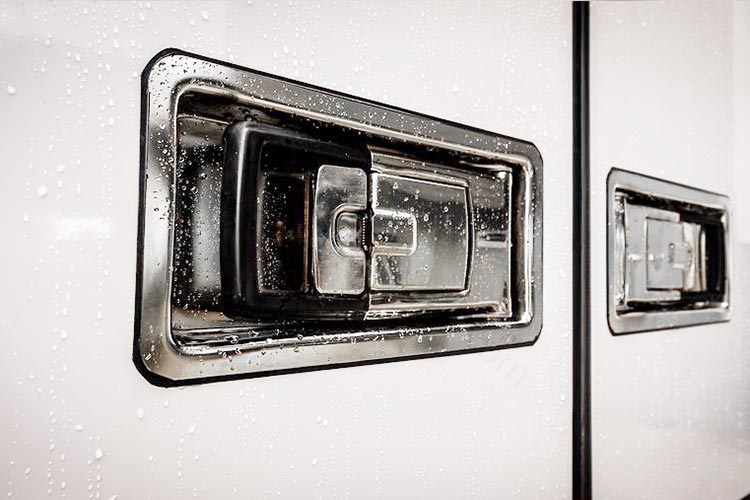
Advanced Door Lock System
Safe and reliable, easy to operate, and effectively protects the safety of goods.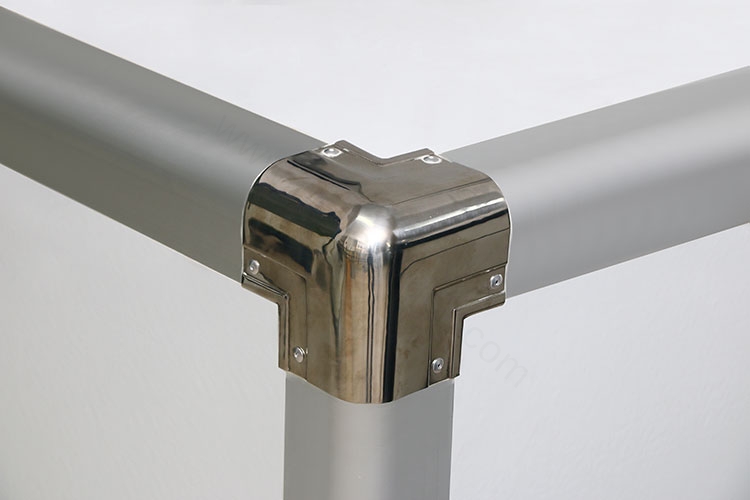
Exquisite Corner Covers and Edging Profiles
Improve the appearance of the vehicle and enhance the stability of the body structure.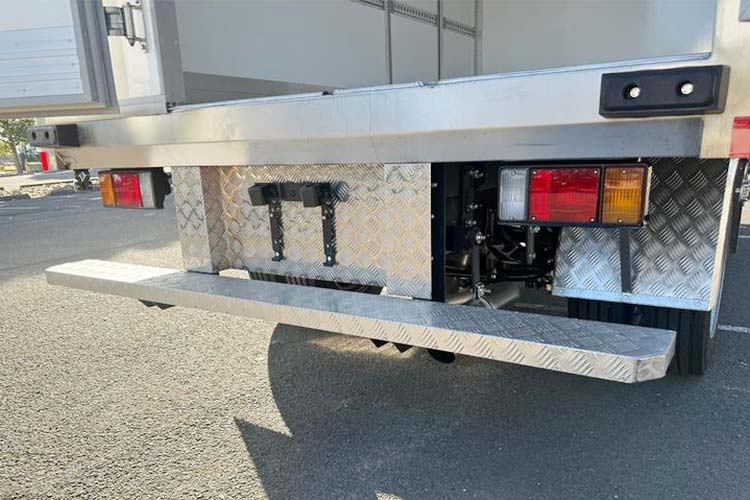
High-Brightness Safety Lights and Bumpers
Improve driving safety at night and in bad weather.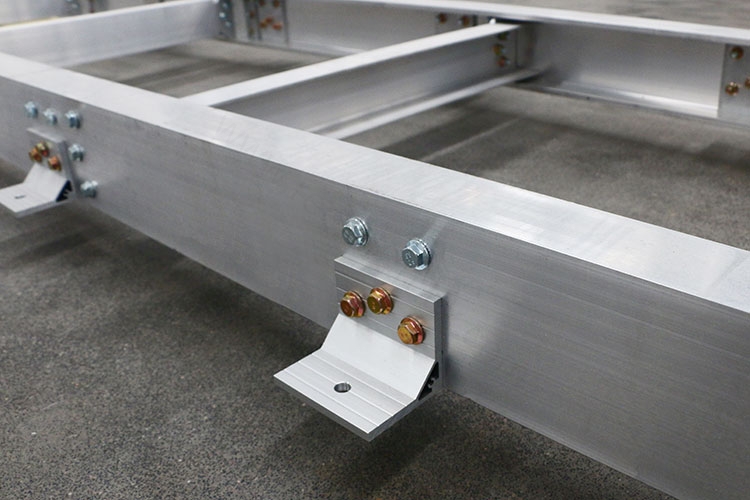
Optimize Subframe
Ensure smooth driving of the vehicle and extend its service life.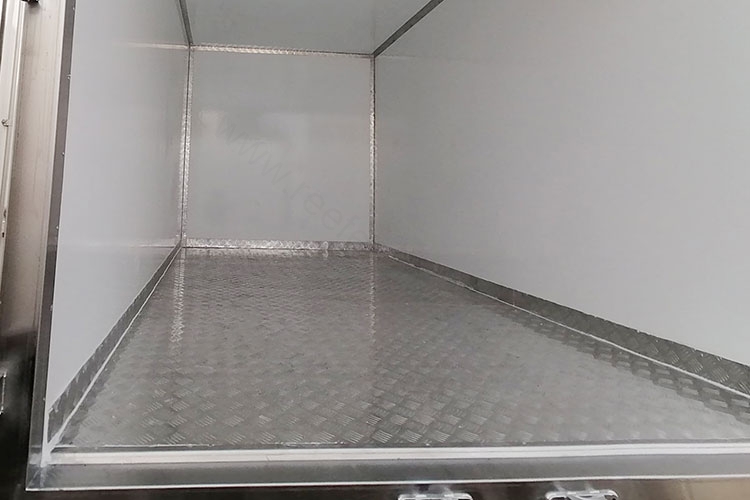
Laminated Floor Structure
Strong load-bearing capacity, non-slip and wear-resistant, easy to clean and maintain.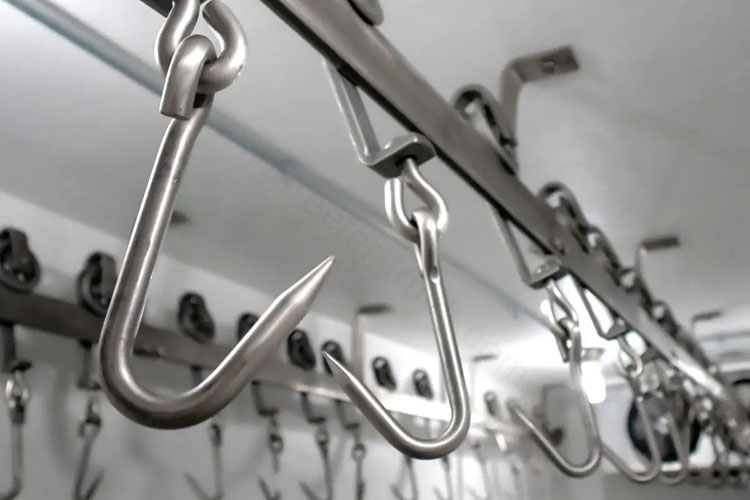
Suspension System
The structure is stable and can bear a large weight.Packaging Solutions
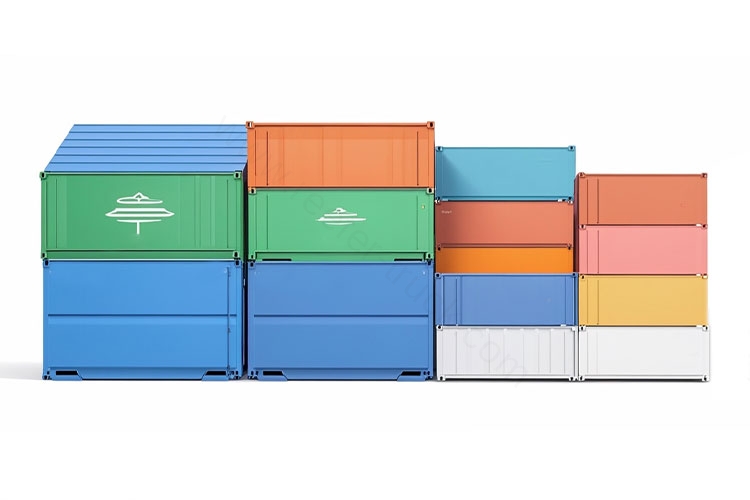
Our Strengths
With 20 years of experience in truck design and development, we have a team of more than 100 professional manufacturing elites who continuously promote product optimization and upgrading with superb skills and innovative thinking.
In order to serve global customers, we are equipped with an international service team composed of multilingual experts, proficient in more than 10 languages including English, Russian, French, Spanish, Portuguese, Arabic, German, Italian, Japanese and Korean, ensuring unbounded communication and considerate service.
So far, we have successfully established long-term and stable cooperative relationships with customers in more than 50 countries and regions around the world. This is not only a recognition of our product quality and design capabilities, but also a source of motivation for us to keep moving forward.
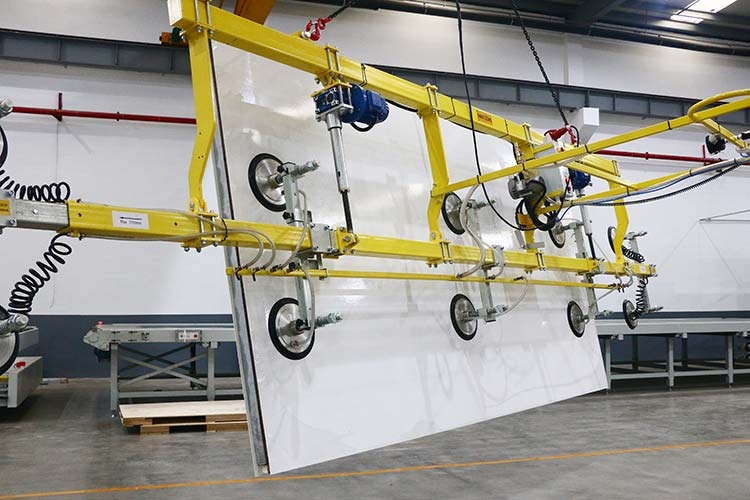
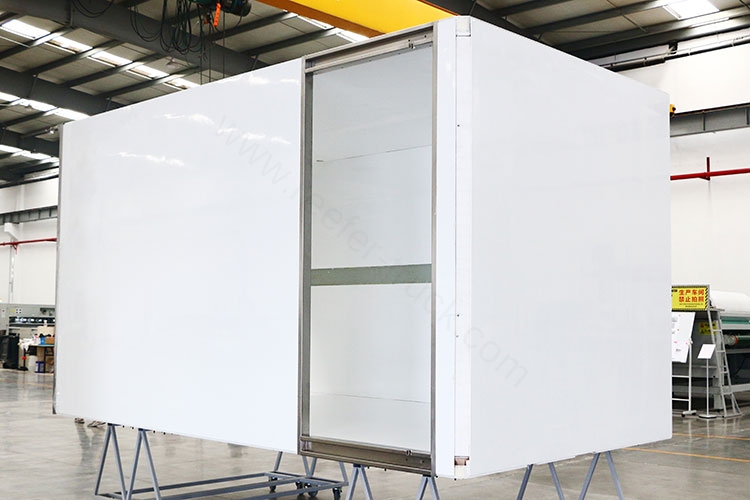
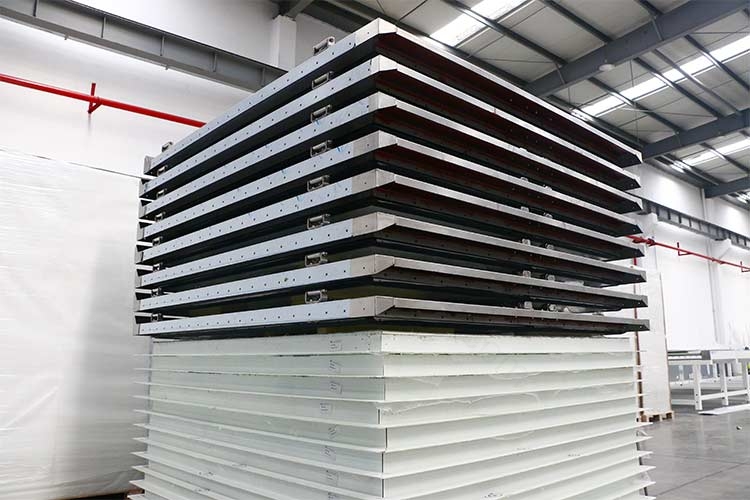